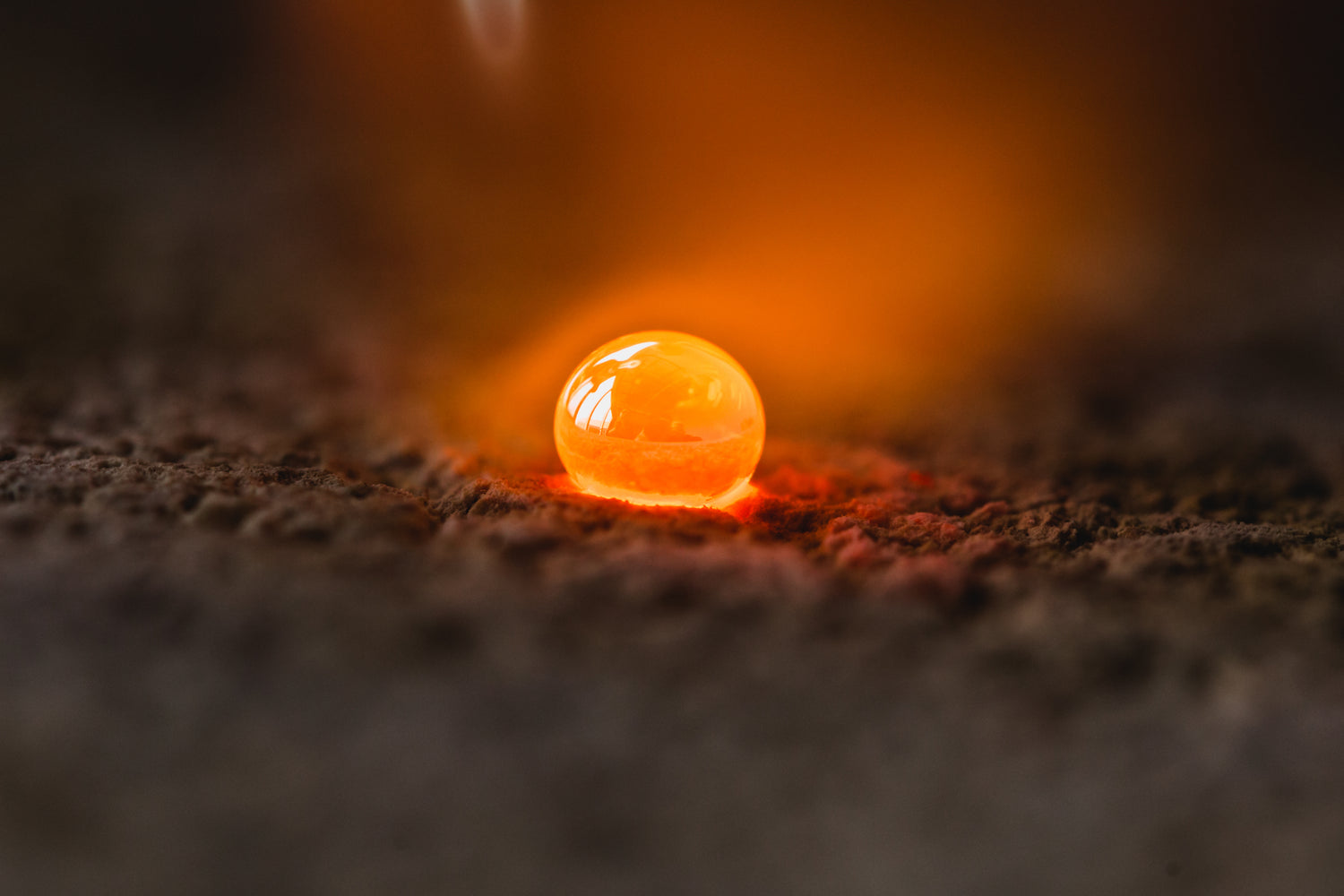
Metal Work and Fabrication Services
ACE Welding originated in 1989 and has since become renowned for its expertise in steelwork and custom-made fabrications. Our extensive knowledge allows us to offer exceptional fabrication services for railings, staircases, gates, and security bars. In addition to that, we provide restoration services and specialise in unique welding projects. As your local specialists located in the South West of England, ACE Welding is your go-to choice for custom welding and fabrication services.
Our services
Frequently Asked Questions
What are the 4 main types of welding?
- MIG (Metal Inert Gas) Welding: Also known as GMAW (Gas Metal Arc Welding), MIG welding uses a continuous consumable electrode wire that is fed through a welding gun, along with a shielding gas, to melt and join two pieces of metal together. It is commonly used for welding steel and other non-ferrous metals, and is known for its versatility and ease of use.
- TIG (Tungsten Inert Gas) Welding: Also known as GTAW (Gas Tungsten Arc Welding), TIG welding uses a non-consumable tungsten electrode to produce the weld, and a separate filler metal may be used if required. TIG welding produces high-quality, precise welds and is commonly used for welding thin materials, stainless steel, aluminium, and other exotic metals.
- Stick Welding: Also known as SMAW (Shielded Metal Arc Welding), stick welding uses a consumable electrode coated with flux, which generates a shielding gas when it melts to protect the weld from atmospheric contamination. Stick welding is versatile and can be used for welding steel, stainless steel, cast iron, and other materials, making it a popular choice for construction, fabrication, and maintenance work.
- Flux-Cored Arc Welding (FCAW): Flux-cored arc welding is similar to MIG welding, but instead of a solid wire electrode, it uses a tubular wire filled with flux, which generates a shielding gas to protect the weld. FCAW is known for its high deposition rates and is commonly used in heavy-duty applications, such as in shipbuilding, construction, and pipeline welding.
Note: There are several other welding processes and variations, but these four are some of the most commonly used and well-known types of welding.
Which weld is the strongest?
The strength of a welded joint depends on various factors, including the type of welding process used, the materials being welded, the joint design, and the skill and technique of the welder. In general, the strength of a welded joint is determined by the quality of the fusion between the base materials and the filler metal, as well as the absence of defects, such as porosity, cracks, or incomplete penetration.
In terms of tensile strength, TIG welding and MIG welding are generally considered to produce high-quality, strong welds. TIG welding, in particular, is known for producing high-strength welds with excellent fusion and minimal distortion, making it suitable for critical applications where weld strength is a top priority. TIG welding is commonly used for welding materials such as stainless steel, aluminium, and other exotic metals that require high-strength welds.
However, it's important to note that the strength of a weld is not solely determined by the welding process, but also by other factors, such as proper joint preparation, appropriate filler metal selection, and skilled welding technique. Each welding process has its advantages and limitations, and the suitability of a particular welding process for a specific application depends on various factors, including the type of materials being welded, the joint design, the required strength of the weld, and other considerations. Consulting with a qualified and experienced welding professional is recommended to ensure the appropriate welding process is chosen for a specific application to achieve the desired strength in the welded joint.
What are the 7 basic welding types?
The number of welding processes may vary depending on the criteria used for classification, and different sources may categorise welding processes differently. However, here are some commonly recognised and widely used welding processes:
- Shielded Metal Arc Welding (SMAW or "Stick" Welding): This process uses a consumable electrode coated with flux that creates a shielding gas when it melts to protect the weld from atmospheric contamination. It is commonly used in construction, fabrication, and repair work.
- Gas Metal Arc Welding (GMAW or "MIG" Welding): This process uses a continuous consumable electrode wire that is fed through a welding gun, along with a shielding gas, to melt and join two pieces of metal together. It is widely used for welding steel, stainless steel, and aluminium, and is known for its versatility and high productivity.
- Gas Tungsten Arc Welding (GTAW or "TIG" Welding): This process uses a non-consumable tungsten electrode to produce the weld, and a separate filler metal may be used if required. It is known for producing high-quality, precise welds and is commonly used for welding thin materials, stainless steel, aluminium, and other exotic metals.
- Flux-Cored Arc Welding (FCAW): This process is similar to GMAW, but instead of a solid wire electrode, it uses a tubular wire filled with flux, which generates a shielding gas to protect the weld. FCAW is known for its high deposition rates and is commonly used in heavy-duty applications.
- Submerged Arc Welding (SAW): This process uses a continuously fed electrode that is submerged in a layer of granular flux, which creates a protective covering for the weld. SAW is commonly used for welding thick materials and producing high-quality, high-deposition rate welds, particularly in heavy fabrication and structural applications.
- Oxy-Fuel Welding (OFW): This process uses a mixture of oxygen and fuel gas, such as acetylene or propane, to create a high-temperature flame that melts the base metal, and a filler rod may be used to create the weld joint. OFW is commonly used for welding thin materials, heating, and cutting applications.
- Resistance Welding: This process uses the resistance to electric current flow in the workpieces to generate heat, which melts the materials and forms a weld. Resistance welding methods include spot welding, seam welding, and projection welding, among others. Resistance welding is widely used in manufacturing and automotive industries for joining sheet metal components.
These are some of the commonly used welding processes, but there are many other specialised welding processes and variations depending on specific applications, materials, and requirements. Each welding process has its advantages, limitations, and suitable applications, and the choice of welding process depends on various factors, including the type of materials being welded, the joint design, the required quality of the weld, and the skill and experience of the welder.
Can you get shocked welding?
Yes, welding involves the use of high electrical currents, and there is a risk of electrical shock if proper safety precautions are not followed. Electric arc welding processes, such as Shielded Metal Arc Welding (SMAW), Gas Metal Arc Welding (GMAW or "MIG" welding), Gas Tungsten Arc Welding (GTAW or "TIG" welding), and Flux-Cored Arc Welding (FCAW), all use electrical power sources to generate an electric arc that melts the base metal and forms the weld.
During welding, the welding machine produces high electrical voltages and currents that can be hazardous if not handled properly. Direct contact with live electrical parts or conductive materials can result in electric shock or electrocution, which can cause serious injuries or even be fatal.
To minimise the risk of electric shock while welding, it is crucial to follow appropriate safety measures, including:
- Properly grounding the welding equipment and ensuring that the electrical connections are in good condition.
- Using appropriate personal protective equipment (PPE) such as insulated gloves, boots, and clothing to protect against electric shock.
- Avoiding contact with live electrical parts, conducting materials, or water while welding.
- Ensuring that the workpiece and the welding equipment are properly insulated from ground and other conductive surfaces.
- Properly training and qualifying welders to handle welding equipment safely and follow safe welding practices.
It is important to receive adequate training and follow proper safety guidelines when welding to minimise the risk of electrical shock or other welding-related hazards. It is always recommended to consult and follow the relevant safety regulations, codes, and standards in your area or workplace to ensure safe welding practices.
